Improving construction efficiency.
After 24 years in the design and construction industry, I sit back and look at how much money is thrown away due to waste. There are many things that contribute to waste, and I have observed it first hand in large companies, as well as in my own custom design & construct company. Sadly, I believe that we waste 30% on every project and construction efficiency from the start is where we all could improve.
Waste is more than what we throw in the bin.
Where are we wasting money, and where could we improve construction efficiency? Firstly, it is important to look at where waste create is created. Many assume that waste is simply due to design process inefficiencies, or over-orders. In fact, most of us conclude that the rubbish that is thrown in the bin on site is the largest percentage of waste. However, it’s simply not true. In my experience, over/under-ordering & incorrect order-waste, accounts for merely 5% waste for volume builders & 10% waste for custom home builders. Although the percentage is small, this waste is still not acceptable and can easily be halved with the right technology.
Too many plans.
I believe a large percentage of waste (10% to 15%) is due to communication, documentation and time management inefficiencies. A set of plans with 40 or more pages is waste, it wastes design & drafting time, estimators time, the builders time, and the engineers time. Moreover, it dramatically increases the chance of error. So why do we do it? Unfortunately, our industry does not adapt to change or embrace technology. We (the design, construction & manufacturing industries) are all guilty of doing it the same way over and over again. The mentality is: if it kind of works, why change it? And without a feasible, hassle-free solution, most would tend to agree. However, I will never be okay with waste – we have the capacity and technology to evolve for the better. Now is the time to look at the possibilities, and change our industry. I believe that 3D Virtual Design and Construction, BIM models, is the answer to construction efficiency.
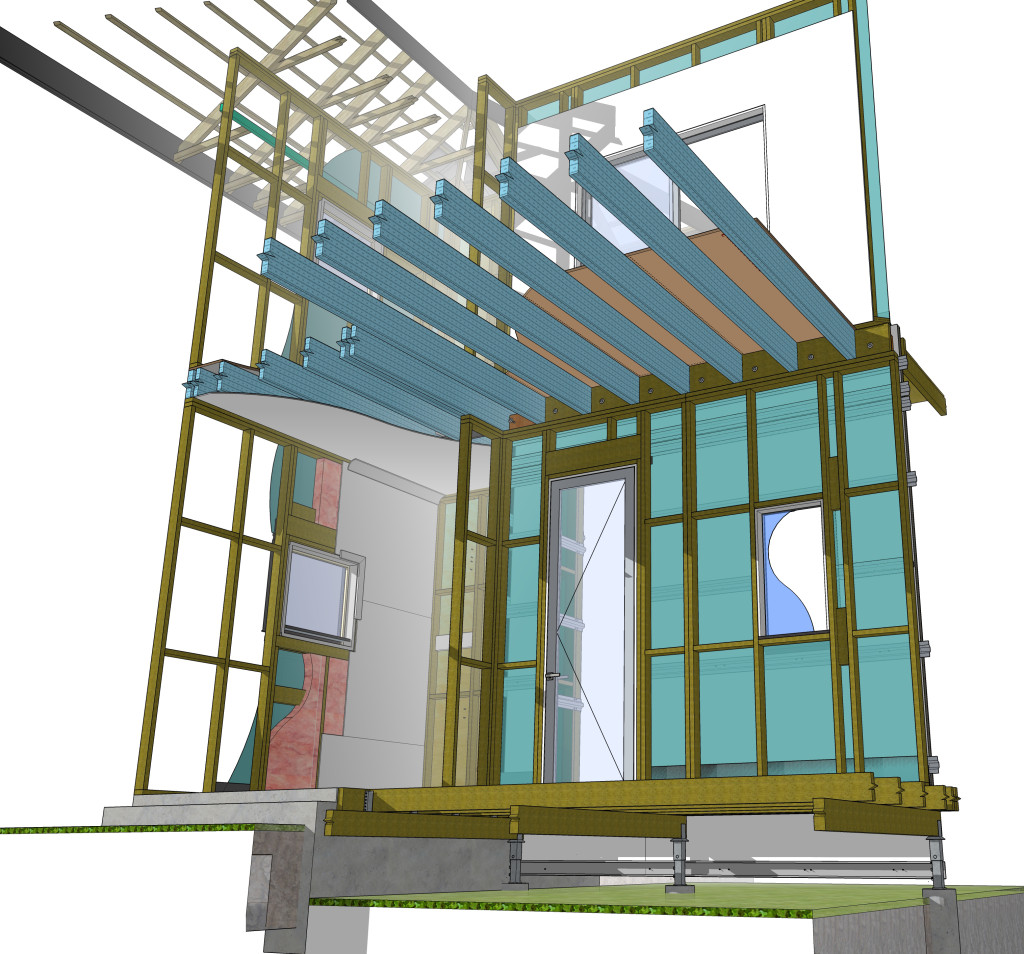
Waste is included as contingency. Why?
Before I discuss how we can reduce this waste with Virtual Design and Construction & BIM , there’s a large percentage of waste that’s yet to be discussed. A large portion of waste is derived from the way that we perform a Bill of Materials. Smaller builders can spend 40 hours (or more) of unpaid work to undertake a BOQ. Once the take off is compiled and a final figure is reached, it’s presented in the form of a preliminary quote or price. The price is either accepted or rejected, and for the lucky tenderer, the job proceeds to a contract. However, an average project has up to 3 to 5 builders tendering on the job, for free. That is approximately 200 hours of unpaid work. Now that is some major waste.. Moreover, if the successful tenderer gets a contract signed and proceeds to construction, all of the information that was compiled for the quotation must now be added to a project management application, and also an accounting program. Believe it or not, this is not a click of a button, and in the majority of cases, a builder will spend another 40 to 400 hours to finish this work. Is anyone seeing my point here? This is direct waste, it cannot be recouped, construction efficiency it’s not. It’s also worth noting, the client essentially pays for this wasted time, as it’s add as contingency into their margin, to cover some of their losses. This is a global problem, and it’s costing our industry trillions of dollars.
It is true, the design Industry and Construction Industry are beginning to embrace Building Information Modelling (BIM). In fact, some governments across the world have now mandated BIM on public infrastructure. However, large construction project case-studies have shown that BIM has resulted in less than a 5% saving.
We need more than just BIM.
I believe, if BIM is to truly change our Industry for the better, it needs to be combined with Virtual Design and Construction (VDC) and Estimating. Imagine if Builders could quote directly from a comprehensive 3D Virtual Design and Construction model? This would be the ultimate in construction efficiency and a huge advantage to industry as a whole.
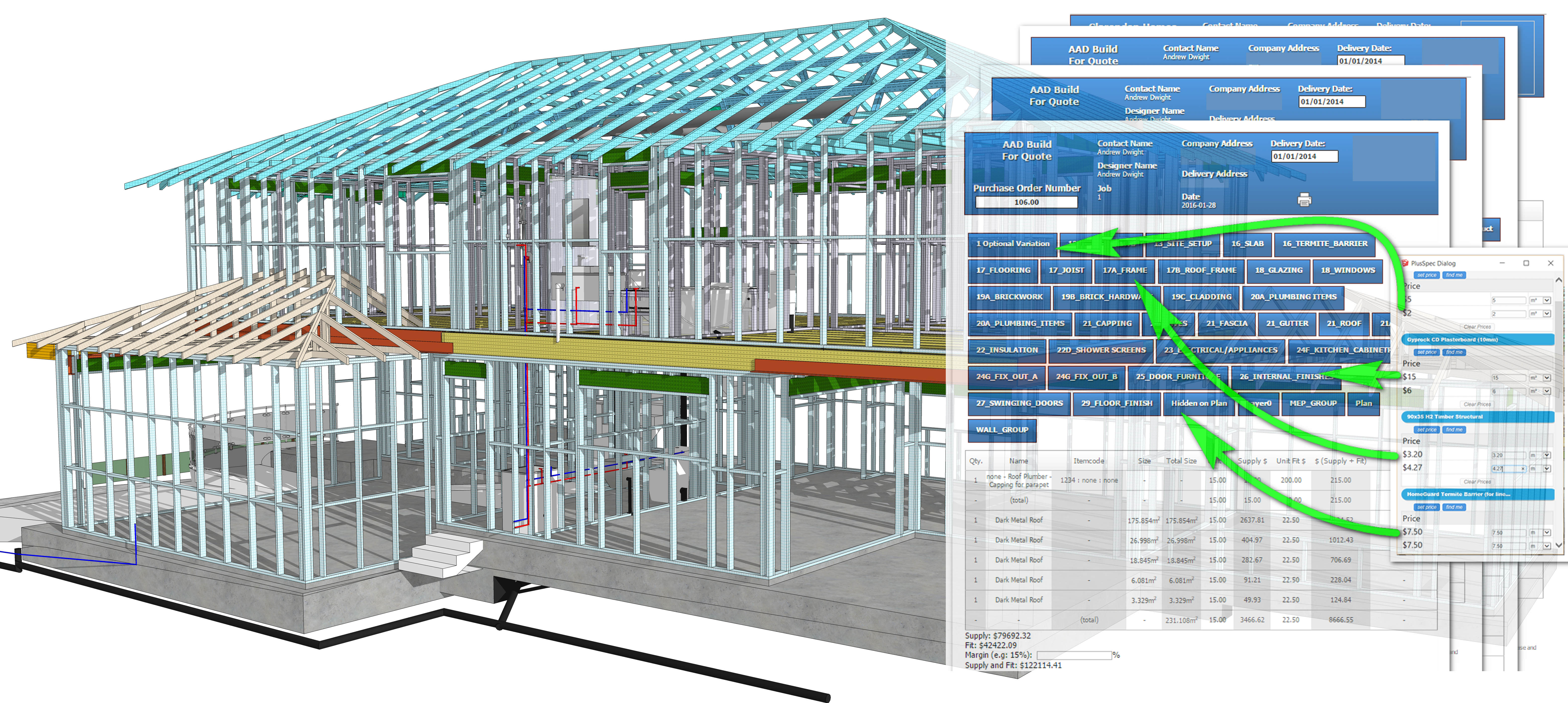
The technology is available.
We already have the technology to create a 3D model (in various iterations). However, for some silly reason, we return to antiquated practices by spending endless hours converting it into 2D, just to print it as a huge plan set. This is where the waste percentage rises again & construction efficiency suffers. The tail-end contractors may not have seen the 3D model or understood the project’s complexities. And in many cases, even the engineers will not see it in 3D. In my opinion, Project Stakeholders, as well as the trades should be able to analyse the 3D model at any time (especially on site). I believe that this would lead to far less errors, waste and increase construction efficiency by up to 30%.
More than Just a 3D model.
I’ve trouble understanding why 3D models are used as nothing more than a new way to create 2D plans! I can only assume the designer has IP, or liability concerns. If there is a problem, and if the latter is indeed the reason, this leads me to Integrated Project Delivery: ‘IPD’ (stay tuned for our upcoming IPD article). Essentially IPD is where the Designer, Engineer, Client and Builder, all assess the 3D model and collaborate on the best outcome. The main thing to be taken from this is that the liability is now spread over the participants, and not wholly and solely placed on the designer. It also gives contractors the ability to be up front and charge for all work done instead of adding it as contingency in their margins. Most importantly, 3D allows project stakeholders to truly understand the design intent, and easily accommodate for specific complexities.
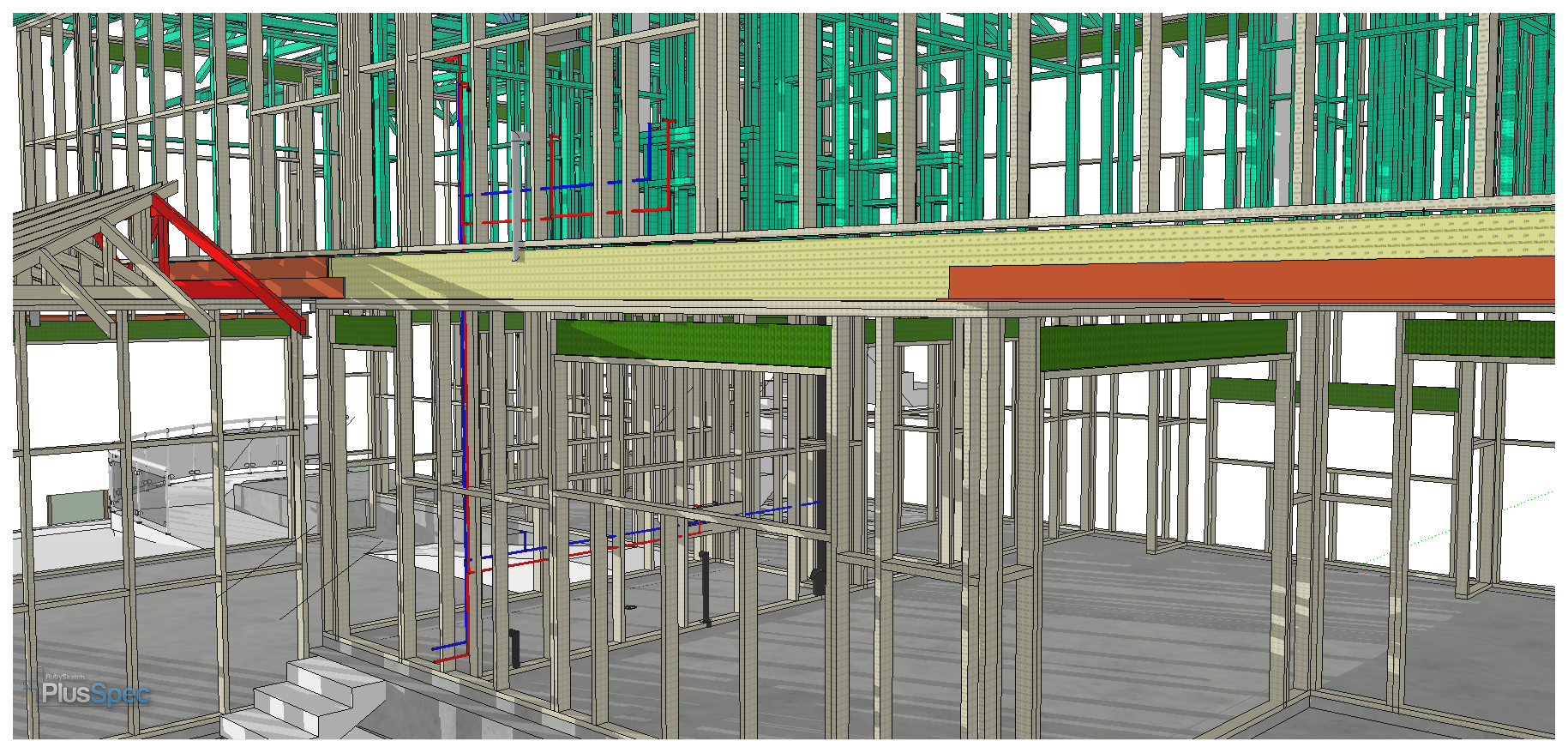
BIM by itself is not enough.
If our Industry is to reduce waste, we need to incorporate construction efficiency via 3D Virtual Design and Construction, BIM & Estimation, in a Design and Construction Delivery Model:
- Designer preliminary design 3D. (Paid)
- Designer uploads model to cloud & sets permissions for access. (Paid)
- Client agrees/ comments on design.
- Engineer has a preliminary preview and comments. (Paid)
- Tendering builders & or Sub Contractors have a preliminary preview and comments. (Paid)
- Designer compiles and replies to tagged comments, which have been saved in the draft 3D model. (Paid)
- Client agrees on aesthetic changes due to feedback (if any).
- Engineer adds in structural detail. (Paid)
- Builder & or Sub Contractors A,B,C etc. receive model and perform 1click quantity take off’s, and associate prices. Comments if required. (Paid)
- Builder agrees model is complete, or comments. (Paid)
- Builder submits tender price.
- Authorities are informed of development application and also view model: shadows and neighbouring properties notification. Basic model is shared and approval is given, or objections are sent to designer.
- Designer & client choose winning tender.
- Builder adds 1 click take off to accounting software.
- Builder builds from model, and a small 2D set (if required).
When a Design and Construction Delivery Model, such as the above, is implemented on all size projects, the industry will see huge cost savings and massive reductions in waste (of all kinds).
The Results.
As we get more technologically advanced, time will being freed up and not chewed up in retrofits and last minute plan re-issues. 2D document delivery is ‘old hat’. It’s time to embrace the future by actually utilising the 3D model at every stage of a project.
On a closing note, here is the icing on the cake: When a project is delivered in such a way that it has all of the information saved in the 3D model, ongoing facility maintenance and alterations will no longer require redraws (as-builts) or structural adequacy reports. These are the number one contributing factors when it comes waste in the renovate extension sector of our industry.
A 3D model has the capacity to be the communicator of past and present design and construction information. It is the vault in which all information can be stored & found efficiently, at any point in time.
I have spent the last 9 years of my life creating a solution for construction efficiency. I’d be interested in hearing your thoughts.
All the best for 2016.
Andrew Dwight,
🙂
Leave a Reply
You must be logged in to post a comment.