If you’ve listened to Episode 2 of our Architects are from Mars Builders are from Venus Podcast, then you would have heard Ross Beattie (a builder with over 20 years in the construction industry) say “You don’t want air-conditioning shafts coming through your trusses/rafters, and we’ve all seen that. It’s hard for a tradesman to see his good work getting butchered for a pipe.”
And we 100% agree.
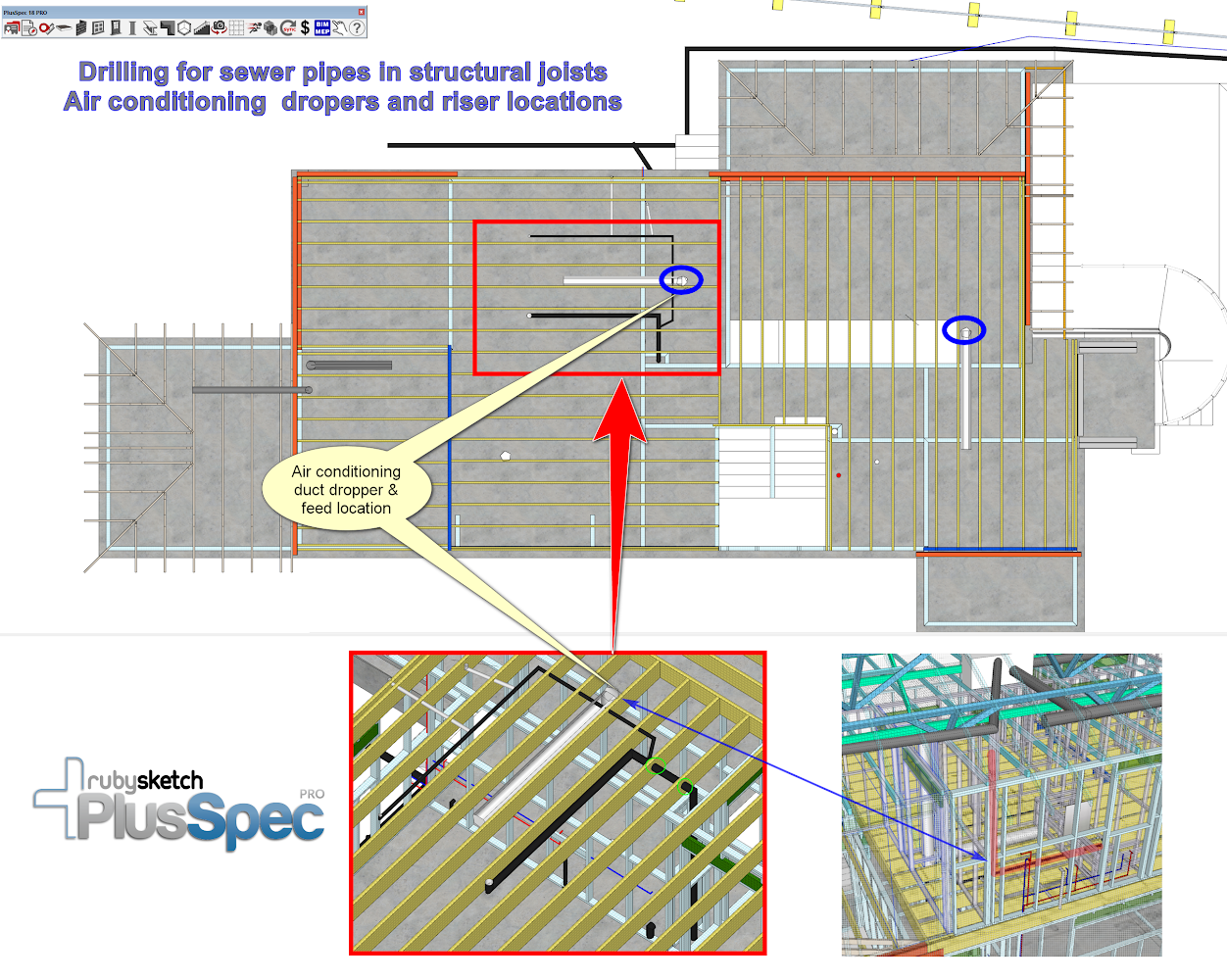
In this post, we are going to discuss how MEP (Mechanical, Electrical, Plumbing) is one of the main causes of structural ‘butchering’, which costs the Residential design and construction industry time, money and waste. Although similar issues happen on commercial projects, MEP engineers are generally engaged to solve these conflicts (at substantial cost). Therefore, errors in commercial projects aren’t as prevalent.
However, Residential housing is different. In most residential projects MEP consultants are not engaged, and when the plans leave the hands of the Architect or Designer, they end up in the hands of an individual vendor, rep or supplier – who only supply individual pieces of the project (such as joists, bricks, windows, AC, etc). And although MEP is specified, the responsibility for the MEP, such as how the AC or plumbing is run (including the tolerances) is typically left to the contractor or vendor/rep/supplier.
If a design has the joist and frame locations worked out before construction commences the frames, joists and trusses go up very quickly and efficiently. But then when it’s time to add the MEP – BAM! “Houston, we have a problem.” One of the biggest issues with residential projects is that the MEP is not detailed in the drawings, which VERY often leads to expensive remedial work, or ugly bulkheads and/or cutting of structural members. And yes, this even happens to large volume builders who have built the same home many times!
It is very difficult to capture all of this information in a 2D drawing and to be able to spatially understand the relationship and connection of all materials, in every part of a design. But it’s not just 2D drawings. It’s difficult for most 3D CAD or BIM software also. The reasons are varied, but the simple answer is that the process is normally overcomplicated, or suitable for MEP engineers only (not Architects, Designers or Builders).
That’s why PlusSpec has included a simple, easy to use MEP tool that allows anyone, from the earliest stage of a project, to be able to add the MEP to a design. And because PlusSpec is VDC (Virtual Design and Construction) and also generates all of the structure, it becomes very easy to understand if there are any issues or clashes with MEP and structure. Maximum spans and tolerances will still need to be calculated separately, but because everything is in 3D, it becomes a lot easier to communicate with vendors/reps/suppliers or contractors.
In most cases, structural changes can be done super quickly. For example, you can easily change the joist to a different size, or from one type to another (such as LVL to truss), or even simply changing the joist direction.
We believe that the most successful designs are the ones that scream ‘attention to detail’. And the understanding of materials (aesthetic, structure, tolerances, maximum and minimum spans, and the list goes on) is one of the greatest skills that can be acquired. But, we’ll leave this topic for another post.
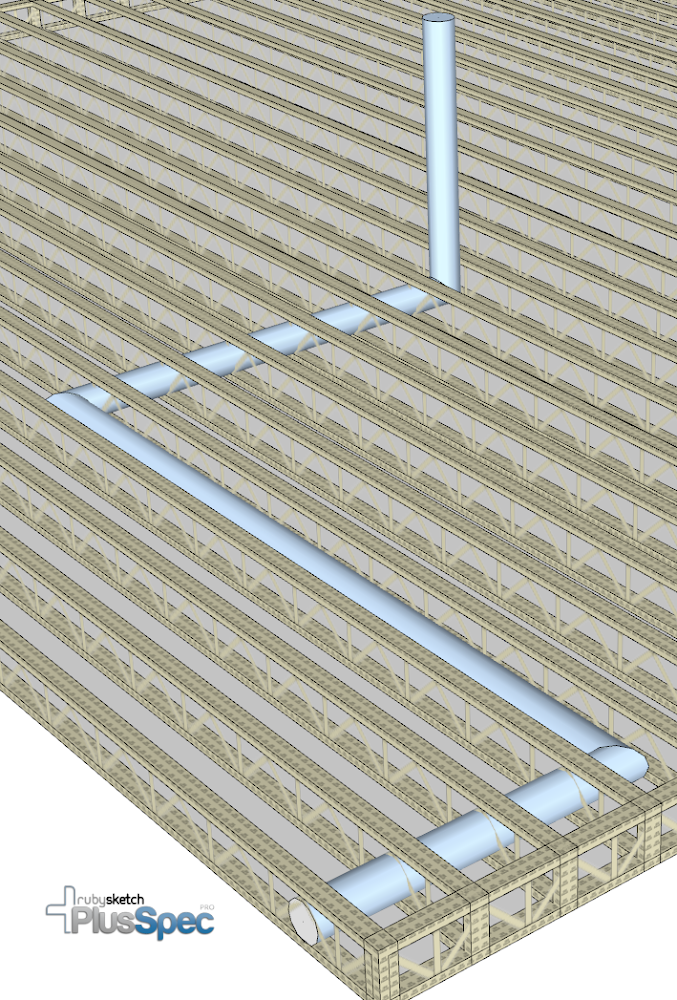
We host the Architects are from Mars Builders are from Venus Podcast because we believe that if everyone in the industry better understands each other, we’ll communicate better – leading to stronger relationships, better built outcomes, and more profitable businesses.
So we hope you’ll join us as we talk to Design & Construction Professionals about their challenges & what they are doing to create amazing businesses. Please subscribe and share some love.
Available on Apple Podcasts (Mac) and Stitcher (Android), on any device and on the go.
Leave a Reply
You must be logged in to post a comment.