It seems everybody is talking about modular construction these days. Some would even say that if you don’t have modular construction on your radar, your business is in danger of falling behind. Well, I don’t know about that – but I do know a thing or two about modular building, and I’m happy to share some of my experiences.
This post dives into lower level detail, tips & help for design, building and delivering modular houses. It’s based on real world experience in real world projects. I am sure by now most understand that Modular Construction/buildings are built off-site in a controlled environment. I’ll do my best not state the obvious.
I encourage designers, builders, engineers and estimators to work together with collaborative tools to achieve a modular Nirvana. If you’ve a passion for modular design and construction this one if for you…
What is modular construction?
‘Modular’ is a very broad term. Technically, a prefabricated frame & truss can be considered to be modular construction, as essentially a manufacturer is joining timber/lumber together in modules that are labeled and numbered so that they can be quickly erected by a tradesperson on site. In saying that, I do not believe the Modular buzz is based on prefabricated frames and trusses. After all, they have been around since Jesus played fullback for Jerusalem.
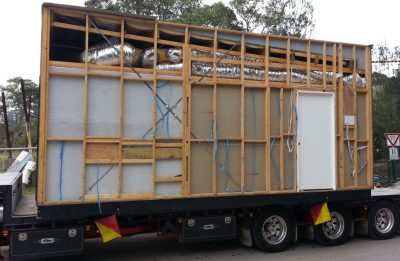
A finished modular home that’s built offsite with everything installed is ideal, yet not always achievable. It seems to me that the ‘New Modular’ is based around adding more, if not everything, to a module. When I say everything, I mean finished products, such as external cladding with paint, structure, wiring, plumbing, internal linings, cabinetry, sun shades, and trimmings. I guess if this is the rationale, why not just build the whole bloody building off site and ship it on trucks? But even this is already being done. I myself have designed and built many projects off site and delivered them in assembled modules. Yet this is not the type of modular everyone is banging on about today.
What construction methods are typical with Modular?
- Traditional stick frame lumber or steel.
- CLT Walls and floors
- SIPS
- TBS
- Cassette floors
- Dincel
- The list goes on
Why Modular Construction?
As industry advances, timelines get shorter, the cost of labour increases and our weather is just as unpredictable as ever. It stands to reason that we need to look at doing more off-site in controlled environments. However, there are more benefits to be gained over and above the obvious time efficiencies. Modular manufacturers can buy materials in bulk for less and store them in convenient places where computer controlled machinery can access it and occupational health and safety can be monitored and controlled more efficiently. I am not saying it is right or wrong that many jobs are going to machines (as that is a topic for another day), but it stands to reason that we now have the technology that enables machinery to pick materials, cut materials and place materials with minimal human supervision, sweat, or risk. As if the writing wasn’t already on the wall, we can buy cars with exceptionally finished mirror coat seamless exteriors, internal combustion 500 horsepower jalopies that will get you from 0 to 100 in under 5 seconds – and most, if not all, come standard with air-conditioned, self-driving, collision-controlled, anti-skid, anti friggin everything, for under 50 grand. But look at the cost of housing around the world – and most of our homes don’t even have hands-free calling, a wide screen LCD, and voice that tells you how you should be running your decision(less) life!
The biggest advantages of modular construction
If you gear it right and set up progress payment schedules, modular construction allows builders to keep a positive cash flow without the risk of the client taking control of the goods on their land. No payment, no delivery.
How many Modular buildings are in existence?
Modular has been around for almost forever. My Grandfather told me of how they used to build Modular back in the second world war. He says the key is to start right and then you will finish right. Oh, and always build in a jig… Bless his soul.
What should architects, designers & builders consider when designing a modular building?
- Most importantly can you get it there? Are there low bridges, load limits on bridges, or transport restriction with authorities?
- Factory capacity. Can the factory deliver the product on time?
- Factory location. Transport plays a factor in cost.
- Longest transportable length.
There are a multitude of trailer sizes, check with your local transport company to confirm sizes
- Longest module length that can be built by the manufacturer.
- Weight per lineal meter/foot.
- Crane set up location.
- Crane type. Mobile or tower crane?
What software can I use to design a modular building?
Modular panel construction has been built to suit existing architecture styling and trends. However, there are huge cost savings to be had when the architect understands more about the methodology. I have a few tricks to show and tell…
I use PlusSpec, as it is built for the purpose. The structure is very important when it comes to modular, drawing walls, floors and rooves that are hollow leaves gaps in estimating and constructability. Weight and size, combined with construction type, play a big part in designing a modular building and PlusSpec fits the task. Very few get it right, mainly because they are using the wrong design platform. I have a friend/associate who also used to use ArchiCAD yet the setup cost and time taken to customise and implement saw projects delayed especially when key staff members took annual leave. An easy to use out of the box solution that can be used by inexperienced staff is recommended to keep the process smooth and efficient.
BIM in Modular
If your designer does not understand what BIM is you should consider getting a new designer or doing it yourself. We can recommend a PlusSpec designer for you yet it is important that you understand that designing and building modular requires input from the 3 main participants after the client has briefed you on the requirements.
- Designer/Architect
- Builder and trades
- Engineers and authorities
What type of input is required?
After the first modular home you build, you will get an understanding of what sizes are easily transportable and manageable. My rule of thumb is one module per truck, and design modules to fit. This is as easy as talking to your transport provider.
TIPS and tricks when designing a modular building
Integrated project delivery (IPD)
Although I believe that Integrated project delivery should pay a part in every project one way or another, IPD is imperative when it comes to Modular. A well communicated modular project from concept to completion is the key to a successful project, that comes in on budget and on schedule.
Who should be present at the meetings? Everyone: the architect/designer, product manufacturers, engineers, builders, crane companies, building supervisor, estimators, the client. However, not everyone needs to be present at every meeting, especially if you are using a Virtual Design and Construction model. Architects and designers need to understand the fundamentals and the concept design should be put together based on these learnings.
Site Preparation for a modular building: what should the builder/ assembler do to ensure efficiency?
Modular construction is a different way of building. It’s not like the traditional method where tolerances can be broad. The main difference with Modular construction is the panels come exactly as per the plan. Well they should anyway. When we set our foundations, footings and slabs, it’s imperative that they are exact, as there is no racking of frames, or grinding, or packing concrete like there is in traditional construction. Remember, there is a 100-tonne crane eating into profit margins here. A supervisor who is strict and fastidious with the ground trades will reap the benefits 10 fold. Spend the time to get the concrete right and allow extra in the budget for grinding high spots and filling low spots before module deliver, because when you start 100% you will finish 100%. It’s important to remember that designers and drafts people are drawing square and level and SIP manufacturers are building to their plans. In many cases nowadays CNC machines are cutting from these drawings and machines simply cannot allow for human error – so we must work to very tight tolerances for modular to be what it has the potential to be.
There is a theme here: start right finish right.
Could a modular building be designed with the old school drafting board,? Sure, yet I would not recommend it. If the reasoning for going modular is to save dollars and increase profits, companies would be contradicting the initial reason for going modular in the first place. You need a solid built for purpose solution. Technology holds the answers for modular, just as it did for the automobile industry. We have the capacity to design off the grid abodes that have more tech than Bill Gates could poke a forked stick at. Think of it as the Tesla of housing. If you are not aware of what Tesla is doing in the car industry, you should take a look at the model S and model x. These jalopies are 100% battery run, and they blow the doors off most, if not all, high-end production sports & super cars (0 to 100 in 2.8seconds) on the market – and they retail for less than the price of a mid range Mercedes. Smart, forward thinking architects, designers and builders should be taking note and adjusting the way we have done things for centuries and look outside the box for a solution that meets the modern world.
Leave a Reply
You must be logged in to post a comment.